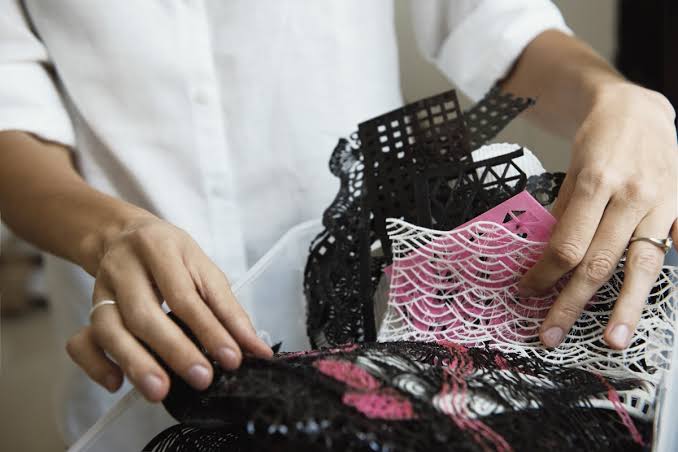
3D Printing – a revolutionary method in designing fabrics
A fabric is made attractive mostly by the designs that appear on it and the creation of designs through printing is one of the easiest ways of doing it. Printing on a fabric or garment is an essential part of the chain in its manufacture. Everything conventionally was thought of in the two-dimension, and it was in the 1990s that experimental work started on 3D or three dimensional printing. It was quite recent, in the last five years one may put it as, that the venture into commercial applications of 3D really began.

But then let us get to know what 3D printing is that everyone seems to be raving about.
The immense possibilities of 3D printing
No! 3D is not something that has sprung round from a corner in recent times. It has been around for some time, but caught the world by storm only in the last few years because of the mind-boggling manner it has begun to be applied in different areas of human endeavour – fashion, architecture, entertainment, industry, bio-medicine, food industry and so many other fields of achievement.

Invented in 1915, it never really came to be taken up full-fledged. A few times in 1950s to 2000 use of 3D technology was made by the entertainment industry but there was nothing worth significant mention. In 2009, the Hollywood movie Avatar made waves with extensive use of this know-how.
In the 1990s, 3D printing techniques were considered suitable only to the production of functional or aesthetical prototypes and, back then, a more comprehensive term for 3D printing was rapid prototyping.

Today, 3D printed objects can have a very complex shape or geometry and are always produced starting from a digital 3D model or a CAD file. There are many different 3D printing processes, that can be grouped into seven categories.
What 3D printing involves
The steps that are followed
- First a 3D model is created on a computer. It is a digital file like a Cad (Computer Aided Design) file. The creation of this 3D model or digital copy of the object is created ground up with
- 1) appropriate 3D modeling software OR
2) based on data generated with a 3D scanner - 3D scanners range from the expensive industrial grade 3D scanners to the DIY (Do It Yourself) scanners that with a little experience can comfortably operate at home.

- 3D modeling software are generally made to suit the functions of the user’s industry. This has resulted in the rise of software that are suited to specific applications. You could get software for as diverse applications as for transportation, furniture design or fabrics and fashion among very many others. There’s industrial grade software that costs thousands a year per license, but also free open source software, like Blender, for instance.

- When one is just beginning the use of 3D, with the amount of choices it could be confusing and a bit overwhelming. Tinkercad (available for free and works in browsers that support WebGL, for instance Google Chrome) is generally recommended. They offer beginner lessons with a built in option to get your object printed via a 3D print service.
- The 3D model is available, now it has to be made 3D printable. This is known as Slicing. In order to make a 3D model printable you have to slice it. i.e. the 3D model is sliced into hundreds and thousands of layers horizontally through a slicing software.
- Sometimes a 3D file can be sliced within a 3D modeling software or in the 3D printer itself. Note: there are cases when a certain slicing tool could be dedicated for a certain 3D printer.
- Slicing being done, it is ready to be fed to the 3D printer. This is done via USB, SD or Wi-Fi. The file that is uploaded in the 3D printer, the object gets 3D printed layer by layer.
- So which printer would be the right choice? A question that one ponders over here is:

Is the hardware important OR should the focus be on the end-result – creating objects? This would therefore lead to whether one should buy a pre-assembled 3D Printer or a DIY 3D printer Kit (that could possible range from $5 at the basic level to $1000000 for very sophisticated applications)
- 3D printer types could be Binder Jetting, Bio, Food, Material Jetting, Material Extrusion, Metal, Powder Bed Fusion with Plastic, Resin, Silicone
3D Printer industry could be any of Aerospace, Automotive, Aviation, Boating, Construction, Consumer Products, Dental, Education, Electronics, Entertainment, Jewelry, Medical, Mining, Sign and Graphics

The lists are growing with time.
The different types of 3D printing
The ISO/ASTM 52900 standard categorized all different types of 3D printing under one of these seven groups:
What then determines the cost of a 3D printer
a) Parts
When a manufacturer uses high quality parts in terms of the motor, frame, electronics, they all add up to the overall cost. This however does not mean that the results are guaranteed to be excellent. A printer with cheap parts could be marketed easily and the results could be great too. But the effort to reach the same level as the former could take quite some time.

b)Research & Development
It takes considerable effort in groundwork and engineering before a certain quality is attained by the manufacturer. This expenditure has to be recovered. Hence the high cost.
c)The Assembly of the 3D Printer
Shipping the parts is much cheaper compared to the shipping of a fully assembled 3D printer. The shipped by parts DIY Kit or semi-assembled 3D printer is assumed to be much cheaper comparatively though it may not always be true since some DIY kits contain high quality parts that even though assembled by you could work out expensive. Some Make it Yourself Kits could take a lot of time and effort in educational tutorials and customer service that could be costly.

d)Customer service & warranty.
When you run into problems with the 3D printer that you just bought from an established brand, there is the reassurance that it shall be attended to. Shipping could entail broken parts, and here one with a warranty would help a lot, even though the initial pricing be on the higher side.

A feel of what 3D Printing can do
Bio-printing
Bio-printing is being used to print tissues and organs to help research drugs and pills. However, emerging innovations span from bio-printing of cells or extracellular matrix deposited into a 3D gel layer by layer to produce the desired tissue or organ. In addition, 3D bio-printing has begun to incorporate the printing of scaffolds. These scaffolds can be used to regenerate joints and ligaments.

3D bio-printing contributes to significant advances in the medical field of tissue engineering by allowing for research to be done on innovative materials called biomaterials. Biomaterials are the materials adapted and used for printing three-dimensional objects. Some of the most notable bio engineered substances are usually stronger than the average bodily materials, including soft tissue and bone. These constituents can act as future substitutes, even improvements, for the original body materials.
In the world of designing
The world of fashion has already experimented with 3D printed shoes, dresses and bikinis besides a whole lot of different designer fabrics. Nike has used it for the football shoe. New Balance is manufacturing custom-fit shoes for athletes. Some companies have been printing consumer grade eyewear with on-demand custom, though the lenses cannot be 3D printed.

The Defense Threat Reduction Agency in the US aims to print mini organs such as hearts, livers, and lungs as the potential to test new drugs more accurately and perhaps eliminate the need for testing in animals.
Food Products
Additive manufacturing of food is being developed by squeezing out food, layer by layer, into three-dimensional objects. A large variety of foods are appropriate candidates, such as chocolate and candy, and flat foods such as crackers, pasta, and pizza.
Lighting
There are quite a few designer lighting fixtures and lamp shades that use 3D printing out there. As of right now, there are no mass production ones. The Dutch company V3RS has its U-TL pendant lamps envelope themselves around a florescent tube, providing a unique shape for lighting solutions. They can take the form of flowers or other shapes that add the extra flavour to the design of any room.

Additive manufacturing has also enabled the development of optics for bulbs and LEDs. Luxexcel’s work in printing optics is already being used for various LED lamps and arrays. It’s altering the way we project and produce light.
Accessories / jewelry
3D printers are great for making trinkets and tiny add-ons for our daily lives. Jewelery printing is perhaps the best example of this. This is another niche within 3D printing. There are some printers that are ideal for creating the wax molds one uses to produce jewellery.

Fashion
3D printing has been on the periphery of the fashion world. Aspiring designers have long been trying to leverage its potential.
Designers are making tools that can shake up the production and retail system. E.g. Danit Peleg is a fashion designer with a keen eye for the future. While implementing 3D printing into fashion is nothing new, the consumer model she is using on her website is immensely clever. On the website, users can design their own jacket and have it printed, fitted and delivered in just a few clicks.

Looking around, one can see the growth of 3D printed fashion.
The Adidas Future craft 4D has a 3D printed sole. Major companies, taking an interest in these possibilities is indicative of an inevitable wave of growth.
Fashion designers have already unveiled shoes and clothing made via 3D printing, in which plastic material is deposited layer upon layer to create a three-dimensional structure.

The advantages of 3D printing

On the flip side
The virtues of 3D printing or the applicability of the technology is indeed revolutionary. As time goes by we shall be seeing more about this wonderful ‘way of doing things’ and transform our lives with their use.

But then let us get to know what 3D printing is that everyone seems to be raving about.
The immense possibilities of 3D printing
No! 3D is not something that has sprung round from a corner in recent times. It has been around for some time, but caught the world by storm only in the last few years because of the mind-boggling manner it has begun to be applied in different areas of human endeavour – fashion, architecture, entertainment, industry, bio-medicine, food industry and so many other fields of achievement.

Invented in 1915, it never really came to be taken up full-fledged. A few times in 1950s to 2000 use of 3D technology was made by the entertainment industry but there was nothing worth significant mention. In 2009, the Hollywood movie Avatar made waves with extensive use of this know-how.
In the 1990s, 3D printing techniques were considered suitable only to the production of functional or aesthetical prototypes and, back then, a more comprehensive term for 3D printing was rapid prototyping.

Today, 3D printed objects can have a very complex shape or geometry and are always produced starting from a digital 3D model or a CAD file. There are many different 3D printing processes, that can be grouped into seven categories.
What 3D printing involves
- The term "3D printing" originally referred to a process that deposits a binder material onto a powder bed with inkjet printer heads layer by layer. More recently, the term is being used in popular vernacular to encompass a wider variety of additive manufacturing techniques.
- It starts with a process of making three dimensional solid objects from a digital file.
- The creation of a 3D or three dimensional printed object is achieved using additive processes. In an additive process an object is created by laying down successive layers of material until the object is created. Each of these layers can be seen as a thinly sliced horizontal cross-section of the eventual object.
- It enables the production of complex functional shapes with the use of lesser material than conventional procedures. The conventional method involves subtractive manufacturing (cutting out / hollowing out a piece of metal or plastic with for instance a milling machine) to get the desired object.

The steps that are followed
- First a 3D model is created on a computer. It is a digital file like a Cad (Computer Aided Design) file. The creation of this 3D model or digital copy of the object is created ground up with
- 1) appropriate 3D modeling software OR
2) based on data generated with a 3D scanner - 3D scanners range from the expensive industrial grade 3D scanners to the DIY (Do It Yourself) scanners that with a little experience can comfortably operate at home.

- 3D modeling software are generally made to suit the functions of the user’s industry. This has resulted in the rise of software that are suited to specific applications. You could get software for as diverse applications as for transportation, furniture design or fabrics and fashion among very many others. There’s industrial grade software that costs thousands a year per license, but also free open source software, like Blender, for instance.

- When one is just beginning the use of 3D, with the amount of choices it could be confusing and a bit overwhelming. Tinkercad (available for free and works in browsers that support WebGL, for instance Google Chrome) is generally recommended. They offer beginner lessons with a built in option to get your object printed via a 3D print service.
- The 3D model is available, now it has to be made 3D printable. This is known as Slicing. In order to make a 3D model printable you have to slice it. i.e. the 3D model is sliced into hundreds and thousands of layers horizontally through a slicing software.
- Sometimes a 3D file can be sliced within a 3D modeling software or in the 3D printer itself. Note: there are cases when a certain slicing tool could be dedicated for a certain 3D printer.
- Slicing being done, it is ready to be fed to the 3D printer. This is done via USB, SD or Wi-Fi. The file that is uploaded in the 3D printer, the object gets 3D printed layer by layer.
- So which printer would be the right choice? A question that one ponders over here is:

Is the hardware important OR should the focus be on the end-result – creating objects? This would therefore lead to whether one should buy a pre-assembled 3D Printer or a DIY 3D printer Kit (that could possible range from $5 at the basic level to $1000000 for very sophisticated applications)
- 3D printer types could be Binder Jetting, Bio, Food, Material Jetting, Material Extrusion, Metal, Powder Bed Fusion with Plastic, Resin, Silicone
3D Printer industry could be any of Aerospace, Automotive, Aviation, Boating, Construction, Consumer Products, Dental, Education, Electronics, Entertainment, Jewelry, Medical, Mining, Sign and Graphics

The lists are growing with time.
The different types of 3D printing
The ISO/ASTM 52900 standard categorized all different types of 3D printing under one of these seven groups:
- Material Extrusion (FDM): Material is selectively dispensed through a nozzle or orifice
- Vat Polymerization (SLA & DLP): Liquid photopolymer in a vat is selectively cured by UV light
- Powder Bed Fusion (SLS, DMLS & SLM): A high-energy source selectively fuses powder particles
- Material Jetting (MJ): Droplets of material are selectively deposited and cured
- Binder Jetting (BJ): Liquid bonding agent selectively binds regions of a powder bed
- Direct Energy Deposition (LENS, LBMD): A high-energy source fuses material as it is deposited
- Sheet Lamination (LOM, UAM): Sheets of material are bonded and formed layer-by-layer

What then determines the cost of a 3D printer
a) Parts
When a manufacturer uses high quality parts in terms of the motor, frame, electronics, they all add up to the overall cost. This however does not mean that the results are guaranteed to be excellent. A printer with cheap parts could be marketed easily and the results could be great too. But the effort to reach the same level as the former could take quite some time.

b)Research & Development
It takes considerable effort in groundwork and engineering before a certain quality is attained by the manufacturer. This expenditure has to be recovered. Hence the high cost.
c)The Assembly of the 3D Printer
Shipping the parts is much cheaper compared to the shipping of a fully assembled 3D printer. The shipped by parts DIY Kit or semi-assembled 3D printer is assumed to be much cheaper comparatively though it may not always be true since some DIY kits contain high quality parts that even though assembled by you could work out expensive. Some Make it Yourself Kits could take a lot of time and effort in educational tutorials and customer service that could be costly.

d)Customer service & warranty.
When you run into problems with the 3D printer that you just bought from an established brand, there is the reassurance that it shall be attended to. Shipping could entail broken parts, and here one with a warranty would help a lot, even though the initial pricing be on the higher side.

A feel of what 3D Printing can do
Bio-printing
Bio-printing is being used to print tissues and organs to help research drugs and pills. However, emerging innovations span from bio-printing of cells or extracellular matrix deposited into a 3D gel layer by layer to produce the desired tissue or organ. In addition, 3D bio-printing has begun to incorporate the printing of scaffolds. These scaffolds can be used to regenerate joints and ligaments.

3D bio-printing contributes to significant advances in the medical field of tissue engineering by allowing for research to be done on innovative materials called biomaterials. Biomaterials are the materials adapted and used for printing three-dimensional objects. Some of the most notable bio engineered substances are usually stronger than the average bodily materials, including soft tissue and bone. These constituents can act as future substitutes, even improvements, for the original body materials.
In the world of designing
The world of fashion has already experimented with 3D printed shoes, dresses and bikinis besides a whole lot of different designer fabrics. Nike has used it for the football shoe. New Balance is manufacturing custom-fit shoes for athletes. Some companies have been printing consumer grade eyewear with on-demand custom, though the lenses cannot be 3D printed.

The Defense Threat Reduction Agency in the US aims to print mini organs such as hearts, livers, and lungs as the potential to test new drugs more accurately and perhaps eliminate the need for testing in animals.
Food Products
Additive manufacturing of food is being developed by squeezing out food, layer by layer, into three-dimensional objects. A large variety of foods are appropriate candidates, such as chocolate and candy, and flat foods such as crackers, pasta, and pizza.

There are quite a few designer lighting fixtures and lamp shades that use 3D printing out there. As of right now, there are no mass production ones. The Dutch company V3RS has its U-TL pendant lamps envelope themselves around a florescent tube, providing a unique shape for lighting solutions. They can take the form of flowers or other shapes that add the extra flavour to the design of any room.

Additive manufacturing has also enabled the development of optics for bulbs and LEDs. Luxexcel’s work in printing optics is already being used for various LED lamps and arrays. It’s altering the way we project and produce light.
Accessories / jewelry
3D printers are great for making trinkets and tiny add-ons for our daily lives. Jewelery printing is perhaps the best example of this. This is another niche within 3D printing. There are some printers that are ideal for creating the wax molds one uses to produce jewellery.

Fashion
3D printing has been on the periphery of the fashion world. Aspiring designers have long been trying to leverage its potential.
Designers are making tools that can shake up the production and retail system. E.g. Danit Peleg is a fashion designer with a keen eye for the future. While implementing 3D printing into fashion is nothing new, the consumer model she is using on her website is immensely clever. On the website, users can design their own jacket and have it printed, fitted and delivered in just a few clicks.

Looking around, one can see the growth of 3D printed fashion.
The Adidas Future craft 4D has a 3D printed sole. Major companies, taking an interest in these possibilities is indicative of an inevitable wave of growth.
Fashion designers have already unveiled shoes and clothing made via 3D printing, in which plastic material is deposited layer upon layer to create a three-dimensional structure.

The advantages of 3D printing
- Construction of a model with contemporary methods can take anywhere from several hours to several days, depending on the method used and the size and complexity of the model. Additive systems can typically reduce this time to a few hours, although it varies widely depending on the type of machine used and the size and number of models being produced simultaneously.
- Traditional techniques like injection moulding can be less expensive for manufacturing polymer products in high quantities, but additive manufacturing can be faster, more flexible and less expensive when producing relatively small quantities of parts.

- 3D printers give designers and concept development teams the ability to produce parts and concept models using a desktop size printer.
- Some additive manufacturing techniques are capable of using multiple materials in the course of constructing parts. These techniques are able to print in multiple colors and color combinations simultaneously, and would not necessarily require painting.
- In the last several years 3D printing has been intensively used by in the cultural heritage field for preservation, restoration and dissemination purposes. Many Europeans and North American Museums have purchased 3D printers and actively recreate missing pieces of their relics. The Metropolitan Museum of Art and the British Museum have started using their 3D printers to create museum souvenirs that are available in the museum shops. Other museums, like the National Museum of Military History and Varna Historical Museum, have gone further and sell through the online platform Threeding digital models of their artifacts, created using Artec 3D scanners, in 3D printing friendly file format, which everyone can 3D print at home.
- Peleg’s first 3D-printed dresses were made of scratchy plastic that bothered the models who wore them. But she found she could use FilaFlex, a flexible, rubbery material that she says “fits the curve of the body really nicely.” Now she can print an entire outfit, including accessories like shoes and sunglasses.
- In contrast, 3D-printed clothes can simply be dumped into blender-like machines that turn the plastics into powder that can then be used to print out something new. And since 3D printing easily allows for custom sizing, the process is inherently frugal with materials.

On the flip side
- Cost is still a matter of concern. Even the smallest home 3D printers run into several hundred dollars. A printer capable of printing human-sized apparel is beyond the reach of individual consumers. And it takes far longer to print an article of clothing than to produce a similar article via weaving or knitting. For example a designer jacket could take about 100 hours to print.
- Then there’s the matter of comfort. Since it’s made of plastic, 3D-printed fabric tends to be stiffer and less comfortable than traditional fabric. So while a 3D-printed dress might be fine on the runway or red carpet, it “doesn’t really make sense yet” for everyday use says an established start-up company in the US.

The virtues of 3D printing or the applicability of the technology is indeed revolutionary. As time goes by we shall be seeing more about this wonderful ‘way of doing things’ and transform our lives with their use.