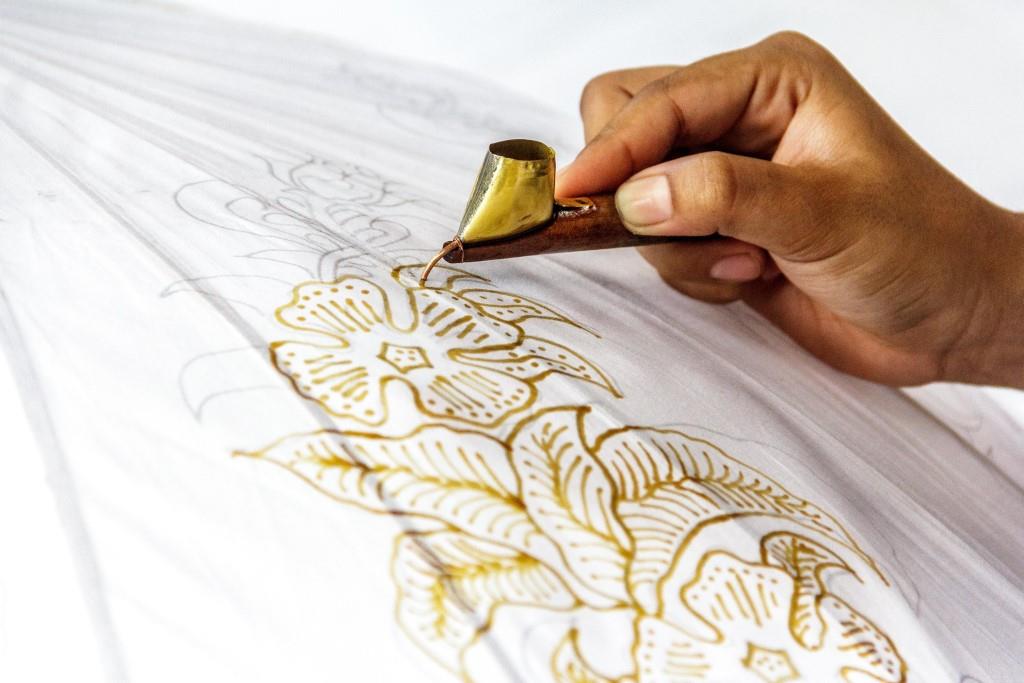
Batik on sarees – a rage at home in India and other places overseas
Batik, also known as ‘wax writing’ is an arty way of decorating fabrics and has come a long way from being a ‘mere handicraft’. A way of decorating cloth by covering a part of it with a coat of wax and then dyeing the cloth, the waxed areas keep their original color and when the wax is removed the contrast between the dyed and un-dyed areas makes the pattern.
In the past, batik was considered as a fitting occupation for aristocratic ladies whose delicately painted designs based on bird and flower motifs were a sign of cultivation and refinement just as fine needlework was for European ladies of similar position.
Beauty lies in Simplicity, and so it is with Batik. One need not be an artist to produce good Batik designs. Some of the best effects in batik are often achieved by chance.
So what is Batik Painting? And what is Batik Printing?
Batik painting is a beautiful ancient art form that involves various figures and patterns drawn on the pieces of fabric. Batik is very often considered a craft like ceramic, pottery or even needlework. Although it is a household word all over the world, batik is still overlooked by art critics who do not consider it an art form.
Batik Tulis (Written Batik)
Batik tulis or Written batik is made by writing wax liquid on the surface of the cloth with a tool called canting. Canting made of copper with a handle made of bamboo or wood. The making of hand-written batik takes approximately 1-3 months depending on the complexity and detail of batik. Because the working techniques are still traditional and manual, making hand-written batik takes longer and is more complicated than other batik techniques. In addition, the fundamental difference between written batik compared to other batik is that there are differences in each pattern, for example, a number of points or curved lines that are not the same because they are made manually by hand. This characteristic of hand-written batik makes hand-written batik more valuable and unique compared to other batiks.
Batik Cap (Stamped Batik)
Batik cap or Stamped batik is batik whose manufacturing process uses a stamp tool. This stamp tool is made of copper plates which form a batik motif on one of its surfaces. Stamp tool or canting cap is made by people who are experts in that field. Making batik with Cap works the same way as using a stamp, but using wax, not ink. This experience process is not easy to do. To make 1 (one) piece of batik cloth, the process of deepening is carried out several times depending on the number of colors desired. Cap is used to replacing the canting function so that it can shorten the manufacturing time. Batik cap is produced from the process of dyeing a tool made of copper which has been shaped in such a way on the cloth. The batik cap motif is considered to have less artistic value because all the motifs are exactly the same. The price of printed batik is cheaper than written batik because it can be made en masse.
The distinctive feature of batik cap can be seen from the repeating pattern/ornament motif. Historically, this batik cap process was discovered and popularized by the brethren as a solution to the limited capacity of batik production if it was only processed with hand-written techniques (batik tulis). The process of making this type of batik takes approximately 2-3 days. The advantages of Batik Cap are easier, faster batik processing, and the most striking of which is the more neat and repetitive motifs. While the drawbacks of Batik Cap include the mainstream design because it usually goes into mass production, in terms of art it looks stiffer and the motifs are not too detailed, and what is certain is the possibility of having the same batik as other people is greater.
Tracing the origin of Batik
Batik paintings are believed to have originated in Indonesia wherein the original word referred to the dots on clothes. It is known when the art of batik was first practiced in Java, batik belonged only to royalty and families of wealth and position. It was a hobby for the royal woman. Aristocrats and royalty had certain designs identifying a family, social status or geographical location on the island.
Some researchers feel the technique was developed in India then spread out from there since the history of Indian batik can be traced as far back as 2000 years. Indians were conversant with the resist method of printing designs on cotton fabrics long before any other nation had even tried it. Rice starch, and wax were initially used for printing on fabrics. Indonesia apparently took over from India and encouraged the art of batik. With its popularity and success in the western markets, batik became a part of Indonesia.
Interestingly, Batik originated from Egypt in the 4th century BCE. It was used to wrap mummies where linen was soaked in wax, and it was scratched using a sharp tool.
Yet another view has it that the history of Batik is tightly linked to China, made by Chinese artisans who migrated from their motherland where they were using Batik. Silk fabrics imprinted with Batik designs used to export from China through the Mediterranean Sea, therefore, the name “The Great Silk Route.
Anyway it matters little who lays claim to it as long as the world benefits from its propagation.
The popularity of Batik
Noted for its cotton and dyes, India made use of the indigo blue which is the basic color for batik, and one of the earliest dyes. It is believed that after its initial popularity in the past, the tedious process of dyeing and waxing caused the decline of batik in India till recent times.
The revival of batik in India began in the 20th century when it was introduced as a subject at the famous university of Shantiniketan in Calcutta. In the South near Madras, the well-known artist's village of Chola-Mandal is where batik gets an artistic touch. Batik that is produced in Madras is known for its original and vibrant designs.
There are several countries known for their batik creations, starting with India where it originated. After that it moved to Indonesia, Malaysia, Sri Lanka, Thailand and the West.
Let us see what the Batik Waxing process is all about.
Batik waxing is considered an important part of the entire process of batik printing. The common batik fabrics which are used for excellent batik prints are poplin, voiles, cambric, and pure silk.
- The elaborate art of Batik is actually a three-stage process which involves stages like waxing, dyeing and also de-waxing (removing the wax).
- There are other sub-processes as well like preparing the cloths and the designs, where the cloth is stretched on the frame followed by waxing the area of the cloth that does not need dyeing.
- This is followed by preparing the dye, dipping the cloth in the dye and eventually boiling the cloth for removing wax and washing of the dyed cloth in soap.
- The entire process of waxing, dyeing and de-waxing is even repeated multiple times until the whole batik design or fabric is completed.
- The characteristic designs of batik are observed due to the fine cracks appearing in the wax, which ensures that the small amounts of the dye, actually seeps in. It is a feature not possible in any other form of printing. It is very important to achieve the right type of cracks or hairline detail for which the cloth must be crumpled correctly. This requires a lot of practice and patience.
- Knowing how to use the wax is of prime importance. The ideal mixture for batik wax is 30 per cent beeswax and 70 per cent paraffin wax. For first timers even the melted wax of a candle is adequate. It is the skillful cracking that is important. While applying, the wax should not be overheated or it will catch fire. Correct knowledge of colors is also important. Practicing on small pieces of cloth helps in the beginning. Patience is of course a very important factor too.
- The cloth used should be strong enough to bear the heat and wax. Cambric, poplin and voiles are used besides pure silk. Synthetic fabrics should be avoided. Since ancient times Indians have been known to wear vibrant colors and dyes which were made from barks of trees, leaves, flowers and minerals. Blue was obtained from indigo, while orange and red were from henna. Yellow was from turmeric and lilac and mauve from logwood. Black was created by burning iron in molasses and cochineal from insects.
- Since handmade batik is unable to meet with the consumer demands very often the answer is tjanting with a copper block. A tjanting is a metal block made of copper strips introduced into the required design after which it is stamped quickly and with great force.
- Batik making means a process of dying where the patterns are carefully drawn on the fabric with molten beeswax applied from a little copper cup with a fine spout called as the “tjanting” alias teapot. And then the same is dipped in the dye pot.
- The cloth used should be strong enough to bear the heat and wax. Cambric, Poplin, Cotton , and Coils are used besides pure silk. Synthetic fabrics should not be used as they cannot sustain heat. For repetitive designs, in order to save time the wax is applied by metal die or a block made by inserting thin strips of sheet brass in a wooden frame so that the edges of the brass form the desired design pattern. These blocks having a handle are covered with a cloth and are dipped in the molten wax and the excess wax is removed by pressing it against a pad which is kept warm by keeping it near fire of the melting pot. The pattern is thus printed on the cloth instead of being poured on from a small cup out of a spout.
- The wax resist is often combined with block printing. It is easy to apply wax through a stencil either with a brush or using a tjanting. To get the reverse effect by cutting out the pattern on a stiff cardboard or thin metal and then using it as a template, pouring and painting the wax around it leaving the pattern in the original cloth to be dyed later.
- Until recently batik was made for dresses and tailored garments only but modern batik is livelier and brighter in the form of murals, wall hangings, paintings, household linen, and scarves.
Batik features
- Batik wall hangings are considered a hot favourite with the art lovers.
- Traditionally, the Batik paintings are made of dark brown, indigo and white colors, representing the three major Hindu Gods i.e. Brahma, Vishnu and Shiva.
- Batik printed saris, kurtis and wrappers are some of the most preferred choices among the fashion loving people.
- Indian cotton and dyes are considered very popular for use in Batik.
Batik is created in several ways
In the splash method, the wax is splashed or poured on the cloth.
The screen-printing method involves a stencil.
The hand-painting one is used by a Kalamkari-pen.
The scratch and starch resist are the other methods.
Colors and Shades
For example, in Java of Indonesia, the major colors used are Indigo blue and Golden Brown dye made from the bark of the mango tree, Black (which is obtained from combining the two colors) and White. The dying process always goes from lighter to darker shades therefore first Indigo is applied and all the cloth except the blue and the black is covered with wax. Then the color is set by the oxidation process. After which the all the wax is removed by washing the fabric in soap and boiling water mixture, then the fabric is dried and the wax is re-applied on the white and blue painted area which are not supposed to get colored in brown which is used without mordanting. The dyes must be used cold in order to avoid melting of the wax. The fabric is dipped several times in the dye till a satisfied shade is achieved. After the final dyeing, the wax is removed with a hot bath of wood ashes or soap. And then the garment is pressed. And the fabric is ready.
The uniqueness of batik fabric is the crinkled effect due to the braking of wax on the cloth while dying and thereby admitting colors in the protected cloth in fine lines or streaks. This help in distinguishing the wax resist work with the paste resist work which will give a smooth clean white background or if applied lightly would give a uniformly shaded background instead of the irregular lines of color.
Tools required for making Batik designs
Wooden blocks for printing
A vessel for heating the wax
Plastic bowls or buckets to mix the colors
A table with sand on it so that the wax does not spread which helps the design stay consistent throughout and a frame to fix the cloth on to Special brushes are used for making a freehand design.
Batik techniques
- Hot batik consists in the application of melted wax using the special instrument called Tjanting. The process reminds drawing with pencil and it is a very laborious and time-consuming method.
- Cold batik technique uses a special transparent reserving composition, which is a thick mass of rubber origin.
- Cold reserve uses equipment that has a glass tube with a reservoir.
- Free painting involves priming the cloth with saline, which limits the fluidity of paint on fabric.
Modern-day Batik
The striking beauty of batik bedspreads, curtains, tablecloths, and placemats is indescribable. We can get bright colors and the designs. The batik industry is still very much alive today. Although it is common to see the mass production of batik with machines, it is still made by hand in many parts of the world. There is a considerable market for this high-quality cloth.
- Batik is still popular today because of its artistic freedom. The designs become whatever the artist’s heart desires.
- Batik is very durable: it has more colorfastness than printed fabrics because through the dyeing process the fabric absorbs the color so well that it does not easily fade.
- The batik technique first started out as a decoration for royals. Today, the striking and intricate patterns can be seen on the ramp, in the office, and on formal occasions.
A DIY Guide to Batik
Just to give the feel of how Batik evolves on the fabric, here is a simple do-it-yourself project that can be done at home or your classroom with your friends.
Gather Your Materials and Set Up Your Workspaces
Although there is a lot to prep, once things are set up, the process runs fairly smoothly.
Materials
Pencil and Paper
Muslin
Scissors (fabric scissors, if you have them)
Newspaper
Drop Coth, Tarp, or Plastic Sheet
Fabric Dyes
Containers with Lids for the Dyes
Water and Whisk (to mix the dyes)
Beeswax (you can buy specific batik wax)
Crock Pot or Hot Plate and Pot (to melt the wax)
Tjanting Needles
Paintbrushes for Dye
Latex-Free Rubber Gloves (optional)
Large Paintbrush for Hot Wax
Clothes Iron
Workspaces
If you can manage it, divide the areas of work based upon the activity.
1) Drawing Space
2) Waxing Space
3) Dyeing Space
4) Finishing Space
Cut Fabric and Draw
Cut pieces of muslin to size. 9″ x 12″ is a good size for a first project. Tape the fabric to a board or place it on a table or work area. Then, draw the design directly onto the muslin with pencil.
Alternately, place a sketch under the muslin and trace it onto the fabric. The sketches should be as light as possible so the pencil lines do not show through on the final product. Try simple landscapes and animals for a start. Avoid including too many small details.
Apply the First Layer of Wax
Use the tjanting needles to “draw” with liquid wax directly on the muslin. Be aware there are different sizes for different levels of detail. The wax provides a resist, and anything that is covered with it will end up white in the final piece. You may want to try with scrap muslin to practice on, as the tjanting needles take some getting used to. Only when confident you could begin on the final pieces. After you have gone over all of their pencil lines, extra drips, dots, and lines of wax can be added for visual interest.
You could have wax in a small pot on a hot plate, but there are safer and better options. An old crock pot works well–it doesn’t get too hot, and the chance of spilling is minimal.
Add the Dye
After the first wax layer is complete, it’s time to add the dye. Although much traditional batik is placed in a dye bath, you can also use paintbrushes to place color in a specific and detailed way. Painting with the dye is similar to painting with watercolor. However, the muslin does absorb the dye very quickly, so you may want to practice a bit here too. Once you get the hang of it, they’ll enjoy layering and mixing colors.
After mixing according to packet directions, store dyes in well-labeled, covered containers to avoid evaporation. You could cut out the labels from the dye packets and label both the containers and the lids.
Apply the Second Layer of Wax
After the dye is dry, it’s time for the second layer of wax. This time, it is painted over the entire piece of dyed muslin, on both the front and the back. Two coats work best, but you can often get away with one. It is recommended having just one three-inch brush that can cover large areas quickly dedicated to this job. This layer of wax creates a seal over the entire piece, which will be cracked and broken to allow a crackle effect in selected areas.
Complete the Crackle Effect
After the second layer of wax has hardened and cooled, you can begin to work on the crackle effect. Bend and fold the fabric to cause the wax to crack and break. This will allow the black dye to penetrate the wax seal in those specific, cracked areas.
If you are feeling adventurous, you can use latex-free rubber gloves and dip entire pieces into a bucket of black dye. This completes the job quickly, but it will find EVERY imperfection in the wax seal. You may end up with more black on your pieces than you want.
For more precision, simply use a brush to paint or dab the black dye over the cracks. This takes longer but allows a greater measure of control over the amount and placement of the black dye and the crackle effect.
Remove Wax
Removing the wax is simple, but time-consuming. You need to iron, iron, iron…and then iron some more. Have students place the batik in between layers of newspaper, then iron over the piece, allowing the newspaper to absorb the liquid wax as it heats up. Once the newspaper is completely saturated, switch it out for fresh newspaper. It will take numerous repeats to remove all of the wax from the fabric. Once you have removed it all, the piece is finished.
Enjoy the Finished Piece!
Finished pieces can be mounted to a variety of surfaces including cardboard, matboard, and illustration board. To do so, stretch the fabric over the board and glue the edges to the back. Batik is a unique, enjoyable experience from beginning to end. Although it takes a lot of work, you will be thrilled with the results.
Unnati Silks and its wide range of Batik Printed sarees
There have been earlier ranges of Batik Pen that is cumbersome yet comes out beautifully. This range however has a collection of lovely Batik printed sarees where along with some novel designs the fabrics chosen to make the designs upon, also varied. This showed the versatility of the batik that could be applied successfully over different fabrics.
The sarees that were chosen were:
Chanderi sico
Chanderi sarees have been popular for the extremely fine texture and sheer quality. The entry of the new avatar of fusion Sicos (blends in silk and fine cotton) with new designs of Batik have sparked tremendous interest once again. What do we get to see?
Fairly plain to lightly distributed motifs on the body, you also have some with lovely diamond shapes. The borders are extremely eye-catching considering that there are concentric circles in batik or plenty of floral vinery.
Kota cotton
Kota cotton is known for its smooth texture and the well-known khats or squares that appear in the natural weave. There are plenty of bright colors, eye-absorbing colors that may not have much by way of design but definitely the colors chosen are scintillating.
Batik Shibori Kota cotton
While the base fabric remains the same there are bright colored shibori designs that have come out very well on Kota cotton. And there is Batik to provide further interest.
Pure Batik cotton
The quality of the cotton is suitable for the Batik to come out sharply and distinctly in very vibrant colors. Definitely something that should be explored.
Kota Organza Cotton
Organdy or Organza cotton is the sheerest and stiff cotton fabric made with fine spun combed yarns. The fabric is characterized by stiffness and crispness. Most stiff varieties are used in home furnishing fabrics like curtains, but the softer Organdy varieties are used for summer wear like blouses, saris etc. The Batik that has been experimented on this is sensational. On the Khat design beautiful arrays have been printed. Some in the range have single color but in dual shades of light and dark.