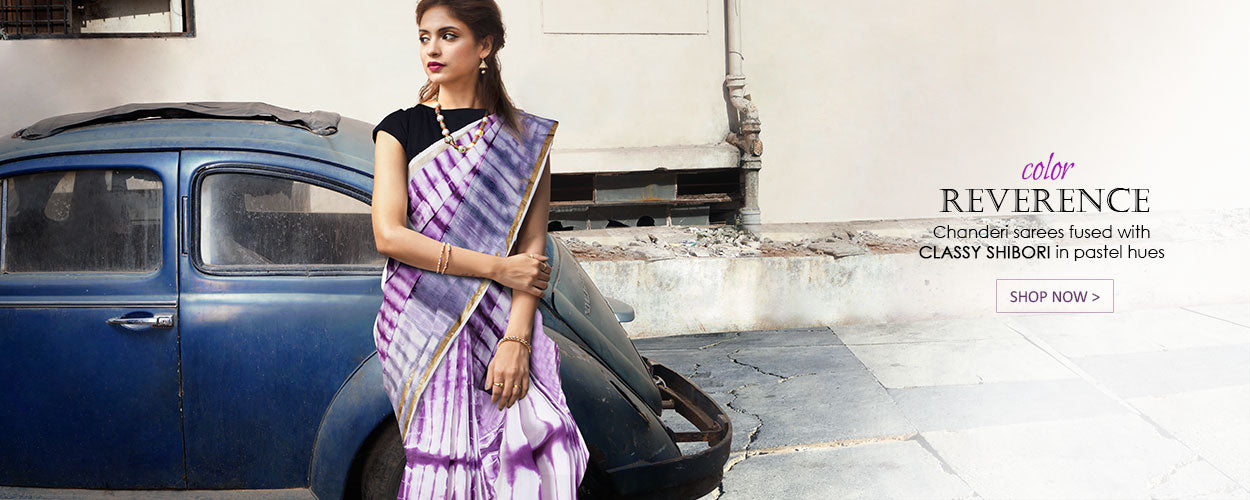
A new wave of Shibori sarees
A traditional style of tie & dye practiced in Rajasthan, India, Leheria (or leheriya) is a wonderful coloring process that produces distinctive patterns on brightly colored cloth. This technique that gets its name from the Rajasthani word for wave, is from the fact that the technique is often used to produce complex wave patterns. Shibori is an off-shoot technique of Leheriya that produces quite similar results.
How did the name Shibori come about?
Shibori comes from the Japanese word shiboru, meaning ‘to wring, squeeze or press’. The technique involves the shaping of cloth and securing it before dyeing. The word ‘shiboru’ stresses on the action performed on cloth, through the process of manipulation on it.
Shibori involves labor-intensive resist techniques that include stitching elaborate patterns and tightly gathering the stitching before dyeing. Patterns are created by wrapping the fabric around a core of rope, wood or other material, and binding it tightly with string or thread before dyeing. The areas of the fabric that are against the core or under the binding would remain un-dyed.
What is special about Shibori?
The resulting patterns of Shibori are soft or blurry edged. These are in contrast to the results from the more sharp edged resists like stencil, paste and wax. Practiced in the urban villages of Delhi, craft clusters of Rajasthan and Bhuj in Gujarat, the technique adopted in india is rope being tied to a bundle of fabric, before applying dye, so that areas covered by the rope do not get colored while those not covered do. Interestingly, Nobel Laureate in Literature, Shri Rabindranath Tagore, who had keen interest in reviving and re-inventing the traditional arts, introduced Shibori to India.
The Shibori process
There are 4 steps in the process – design, stitching, tightening, dyeing.
Design
The design is first conceptualized. Initially there were certain linear and non-linear patterns that formed the basic motif of a shibori design. Now there is a wider choice that can be made from a whole lot of combinations within the basic framework.
A tracing is made on to a sheet of paper or a computer drawing is created which is then transferred to a plastic sheet. This plastic sheet is run through a sewing machine minus the thread. A template with small pin holes is created along the outline of the design. The stencil is then laid on a clean unbleached cloth. A duster dipped in kerosene and silver solution is pressed along it. The solution from the duster seeps through the tiny holes marking the design on the cloth. Kerosene that acts as a binder evaporates shortly. The silver stain is easily removed by washing the cloth.
Stitching
Since the marking is done, a running stitch is manually made with needle and thread along the design. A small cloth is attached at the two ends of the thread that when pulled from both ends, crushes the fabric.
Tightening
Tightening is an important part of the process. Two people are involved in this part of the process. One holds the cloth, the other pulls the thread in opposite directions. The cloth along the thread compresses and a knot is made. The knot is correctly made, else there is every chance of the color seeping into unwanted areas. This is also known as the stitch resist dyeing technique.
Dyeing
When the tightening is done, the fabric is soaked in a mild soap solution or some time. Then it is dipped in a bath before dyeing. The cloth is kept in the bath roughly for 45 minutes.
Preparing the Bath for the dyeing
A thumb rule of material to liquid ratio (MLR) of 1:20 is followed. e.g. 1 Kg. fabric or yarn requires 20 litres of water. The color concentration would be 5 % meaning 50 gm of color to be dissolved in 20 litres of water for 1 Kg of fabric.
In natural dyeing, in order to increase the absorption of color as well as for fastness, the concentration of dye should be increased incrementally. e.g. once the 5 per cent indigo bath is ready and the fabric/yarn has been immersed in it, if a darker shade is required then more indigo should be added slowly (1-2 per cent) till the desired shade is achieved.
For various colors, chemicals are mixed with water and indigo and atmospheric reaction with them yields different results as desired.
Two-color Shibori Process
When there are two shades of indigo to be done, the cloth is first dipped into a vat containing the lighter shade of indigo. After the cloth has dried, tightening is done. It is then submerged in a vessel containing the darker shade of indigo.
The area around the tightened thread gets crinkled and compressed and does not allow the color to leak in, hence allowing that portion to maintain the original lighter shade.
According to shibori, the closer the stitches that are tightened into a knot, the larger will be the area where the color does not seep in. The fabric resists the dye along the stitch.
[/vc_column_text][/vc_column][/vc_row][vc_row][vc_column][vc_video link="https://www.youtube.com/watch?v=9KbArX1x9xI"][/vc_column][/vc_row][vc_row][vc_column][vc_column_text]
Unnati Silks and the Shibori fabrics
Unnati has a love for the bewitching quality of the traditional Lehariya Shibori line of fabrics. There is a captivating line of Shibori in pure handloom Chanderi sico in high quality handcrafted weaves, in white, light and pastel shades of vibrant colors that are captivating and fresh-feel by look and perfectly comfy for the oppressive summer heat.
Borders in consonance or contrast with zari lining, the brightness of the background with the shibori design in vibrant color and the fine count of the weave make it a product that would serve as summer wear for almost any occasion.
Shibori made by the genuine technique bears the pinpricks where the design was stitched in. When held against the light some of the pinpricks made by the needle are visible. This is the hallmark of authentic products that Unnati Silks offers its customers.
Printed shibori passed off as the authentic one can be found out by the lack of pinprick holes when the fabric is held against the light, since prints do not allow light to pass through.
[/vc_column_text][/vc_column][/vc_row][vc_row][vc_column][vc_gallery type="image_grid" images="14749,14751,14750,14752,14753,14755,14756,14757,14754" img_size="medium"]
[/vc_column][/vc_row][vc_row][vc_column][vc_btn title="Shop Online Designer Leheriya Shibori Sarees" color="turquoise" link="url:https%3A%2F%2Fwww.unnatisilks.com%2Fsarees-online%2Fby-work-sarees%2Flaheria-prints.html||target:%20_blank"][/vc_column][/vc_row]