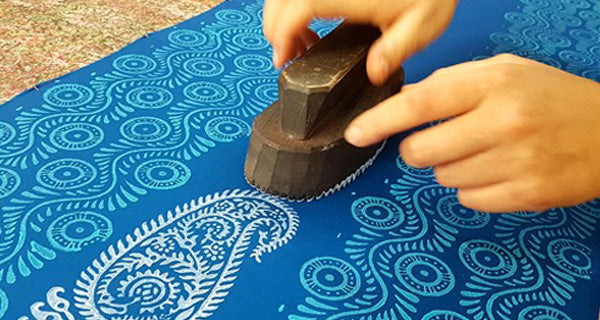
A short story on Printing on Fabrics
Prints on fabrics, is ‘old hat’, but how much do we know about this delightful and quick method of adorning fabrics?
Let us know its travel across time.
What are the advantages of fabric printing over other conventional methods?
- Printing, unlike dyeing, can use many colours to add a pattern on to a piece of woven fabric. Inspiration for these printed designs come from the world around us, with many iconic prints as popular today as they were in the last century.
- Printing designs onto fabric has been around for thousands of years, and although the printing methods have changed our love of patterns remains the same.
How has printing on fabrics originated and what has been its progress over time?
- There is evidence of fabric prints dating as far back as the 4th century BC. The first common method of textile printing originated in China, where examples of woodblock printing from 220 AD have been discovered.
- Both block printing and screen-printing slowly became popular throughout Asia, India and then Europe. During this time little changed in the printing production process as it travelled around the globe.
- In the early 17thcentury the East India Company began to ship printed cotton to England. Unable to produce the designs they wanted themselves, the English also commissioned specific patterns, plainer than the traditional Indian style, to be printed and brought back to Britain. It wasn’t until 1676 that a French refugee set up England’s first print works near to the city of London.
- During the 18thcentury the popularity of Calico printing spread rapidly, with new print-works opening in Switzerland, Germany and later Britain. And it was the French that became most renowned for their artistic patterns and craftsmanship, so popular that they would be copied all over Europe.

- During the industrial revolution these method became mechanized, and cylinder or roller printing was developed. Similar to block printing, but with engraved rollers that could print up to six different colours at once – far faster than anything that had gone before.
- In the 1960s, artist and inventor Michael Vasilantone developed a rotary machine based on screen-printing that was quicker than the traditional flat bed method.
- And today things are even faster – with digital textile printing, using rapid ink jets that not only make the process quicker but also far easier to produce one-off designs.
Why do people love prints on fabrics?
- Technological advances mean that the ways in which we print onto textiles has changed a great deal – but our reasons for doing so have remained the same.
- The human love of pattern and symmetry draw us to beautiful textile prints and want to wear them. For centuries we have been cutting, rolling, pressing and dyeing to make both fabric and its wearer look more beautiful.
What are the three commons methods of commercial textile printing today?
- Screen or stencil printing that uses a cut-out of a stenciled image placed onto a mesh screen. Ink or dye is then pushed through the mesh using a blade onto the fabric below. Screen printing has found to be a better solution when vibrancy of colours is paramount. As the ink is thicker, and is applied in layers, the finished garment is very rich and bright.

Digital Textile Printing, that is also known as direct garment printing, uses specialized inkjet technology. Computer controlled lasers fire high-pressured ink jets directly into the fabric. Digital printing is highly suited to intricate patterns and fine detail as the ink is thinner. Each garment is printed individually, and from a computerized image, which means it is highly customizable. This is fast becoming a very important method of printing.
- But the most common method of textile printing is roller printing – also known as cylinder or machine printing. Pioneered by Thomas Bell in the 18th Century, it’s a similar process to newspaper printing, where the design is ‘stamped’ onto fabric via engraved cylinders. The fabric is pushed through the rollers at terrific speeds, making it an economical method for large amounts of printed fabric.
Which would be a good fabric to print on?
Silk makes an excellent print base, compared to other fabrics. Because it is so pure, no bleaching or other preparations are required before it is printed on.
What are problems that textile printers face in general?
- Different methods of printing come with their own unique peculiarities and problems. Printing on to fabric, especially fine ones, means there is a risk of stretching, and the porosity of the material will also affect the finished result.
- The warp and weft of fabric takes dye differently, so different methods of printing will have different effects on the same fabric.
- Dyes and inks need to be highly suited to the fabric they are being applied to, not just for the look of the garment, the vibrancy, the detail, but also the water fastness, resistance to abrasion, light, and detergents.
- These days, there are often 5 or 6 ‘seasons’ in the fashion calendar. Couple this with demand for more choice of colour and patterns, and printers need to turn their textiles around quickly.
- It’s important to be versatile enough to meet the demands of ‘mass customization’ with shorter print runs and an emphasis on maximizing efficiency and flexibility.
- Digital printing is the method that best suits this demand – it is economical, fast, and has a low ecological impact – and stands up to the consumer driver of mass customization

What are the other forms of Printing?
a) Stencil
Hand stencils, made by blowing pigment over a hand held against a wall, have been found in Asia and Europe dating from over 35,000 years ago, and later prehistoric dates in other continents. After that, stencilling has been used as a historic painting technique on all kinds of materials. Stencils may have been used to colour cloth for a very long time; the technique probably reached its peak of sophistication during the royal period in Japan.
Printing with a press was practiced in Christian Europe as a method for printing on cloth, where it was common by 1300. Images printed on cloth for religious purposes could be quite large and elaborate.
b) Screen printing
Screen printing has its origins in simple stencilling, most notably of the Japanese form (katazome), used who cut banana leaves and inserted ink through the design holes on textiles, mostly for clothing. This was taken up in France. The modern screen printing process originated from patents taken out by Samuel Simon in 1907 in England. This idea was then adopted in San Francisco, California, by John Pilsworth in 1914 who used screen printing to form multicolor prints in a subtractive mode, differing from screen printing as it is done today.
c) Laser printer
The laser printer, was invented in 1969 by researcher Gary Starkweather, who had a fully functional networked printer system working by 1971.Laser printing eventually became a multibillion-dollar business for Xerox.
The first commercial implementation of a laser printer was in 1976, used for high-volume printing of documents such as invoices and mailing labels. It is often cited as "taking up a whole room," implying that it was a primitive version of the later familiar device used with a personal computer. While large, it was designed for an entirely different purpose.
Most noteworthy was the role the laser printer played in popularizing desktop publishing with the introduction of the Apple LaserWriter for the Apple Macintosh, along with Aldus Page Maker software, in 1985. With these products, users could create documents that would previously have required professional typesetting.
d) Inkjet printing
Inkjet printers are a type of computer printer that operates by propelling tiny droplets of liquid ink onto paper
e) Dye-sublimation printing
A dye-sublimation printer (or dye-sub printer) is a computer printer which employs a printing process that uses heat to transfer dye to a medium such as a plastic card, printer paper or poster paper. The process is usually to lay one color at a time using a ribbon that has color panels. Many consumer and professional dye-sublimation printers are designed and used for producing photographic prints.
Later on came Digital printing, which is the reproduction of digital images on a physical surface, such as common or photographic paper or paperboard-cover stock, film, cloth, plastic, vinyl, magnets, labels etc.
It can be differentiated from litho, flexography, gravure or letterpress printing in many ways, some of which are;
Every impression made onto the paper can be different, as opposed to making several hundred or thousand impressions of the same image from one set of printing plates, as in traditional methods.
The Ink or Toner does not absorb into the substrate, as does conventional ink, but forms a layer on the surface and may be fused to the substrate by using an inline fuser fluid with heat process (toner) or UV curing process (ink).
It generally requires less waste in terms of chemicals used and paper wasted in set up or make ready (bringing the image "up to color" and checking position).
It is excellent for rapid prototyping, or small print runs which means that it is more accessible to a wider range of designers and more cost effective in short runs.
f) 3D printing
Three-dimensional printing is a method of converting a virtual 3D model into a physical object. 3D printing is a category of rapid prototyping technology. 3D printers typically work by 'printing' successive layers on top of the previous to build up a three dimensional object. 3D printers are generally faster, more affordable and easier to use than other additive fabrication technologies.
